Complete machine shop
CNC machining of plastic parts enables us to create a wide variety of components with remarkable precision. Thanks to our state-of-the-art machinery and our team of highly qualified technicians, we are able to produce parts to very precise specifications for a variety of industrial sectors.
CNC machining of plastic parts enables us to create a wide variety of components with remarkable precision. Thanks to our state-of-the-art machinery and our team of highly qualified technicians, we are able to produce parts to very precise specifications for a variety of industrial sectors.
Our plastic machining capabilities include:
- Mechanical parts in engineering plastics: Designed for machine tools or specific equipment, these parts can be replacements or components for your products.
- Made-to-measure tools: We manufacture specific tools for particular applications, for both industry and the craft trades.
- Parts requiring multiple operations: We carry out complex 3-, 4- and 5-axis machining.
- Customised front panels : Custom cut-outs for control panels, with engraving and digital printing options.
CNC machining does not require moulds, which means we can produce without minimum order quantities. We can manufacture :
- Single units or prototypes
- Small production runs
- Medium series
- Large series
All at no extra cost.
How does machining plastic parts work?
Machining plastic parts is a manufacturing process that involves removing material from a raw material to obtain the desired shape and dimensions. Here’s an overview of how the process works:
1. Material selection
The first step is to choose the right plastic material for the part to be manufactured. This depends on the mechanical, thermal and chemical properties required for the final application. Commonly used plastics include :
- PMMA (Plexiglass®/Altuglas®): Transparent and rigid, used for optical applications.
- ABS: Impact-resistant and easy to machine, used in electronics and toys.
- PP (Polypropylene): Fatigue-resistant, used in hinges and food containers.
- PC (Polycarbonate) : Highly impact-resistant and transparent, used in safety glazing.
HDPE (High Density Polyethylene) : Resistant to chemicals and abrasion, used in pipes and containers.
2. Preparation of the Raw Part
The plastic material selected is generally available in sheet, bar or block form. These blanks are cut to approximate dimensions to facilitate machining.
3. CNC programming
The machining process is controlled by computer numerically controlled (CNC) machines. Technicians create a CNC programme based on the technical drawing of the part to be manufactured. This program dictates the movements of the cutting tool and the part on several axes.
4. Mounting and fixing
The blank is securely fixed to the machine table using holding systems such as vacuum tables and clamps, or in a chuck for turning operations. Correct clamping is crucial to ensure precision machining.
5. Usinage
Machining can be carried out by various operations, depending on the complexity of the part:
- Milling : Using a rotary cutter to remove material. Can be done on 3, 4 or 5 axes for complex geometries.
- Shooting : The workpiece rotates around an axis, while a fixed cutting tool is used to remove the material. Mainly used for cylindrical parts.
- Drilling and tapping : Creating holes and reaming existing holes. Then tapping so that an object can be screwed in.
The CNC machines carry out these operations according to the pre-set programme, guaranteeing a high level of precision and repeatability.
6. Finitions
After machining, parts may require finishing operations such as :
- Polishing: To obtain a smooth, shiny surface.
- Engraving and printing: To add lettering or logos.
- Assembly: Integration of inserts, fixings or other components.
7. Quality control
Equipped with a three-dimensional measuring machine, at Artois Plastiques each machined part is rigorously checked to ensure that it complies with technical specifications and dimensional tolerances as well as specific shapes. This can also include precise dimensional measurements, strength tests and visual inspections.
Machines and machining techniques
Machining Centre
What is a machining centre?
A machining centre is a versatile CNC (Computer Numerical Control) machine capable of performing various types of operations on metal or plastic parts. Equipped with several tools and axes of movement, a machining centre can perform complex operations such as milling, drilling, tapping and cutting, all in a single or multiple passes of the part.
How it works
Machining centres are designed to receive raw parts and machine them with great precision. The workpieces are fixed on a worktable, and the machine performs the necessary movements following a CNC programme. This programme determines the tool paths and operations to be carried out according to the part specifications.
Benefits
- Versatility: Capable of performing a wide range of machining operations.
- Precision: High precision thanks to digital controls and high-quality tools.
- Efficiency: Enables multiple operations in a single configuration, reducing the need for manual repositioning.
- Cycle time reduction: Thanks to the possibility of programming operations, production times are optimised.
Applications
Machining centres are used in a variety of sectors, including aerospace, automotive and medical device manufacturing. They are ideal for producing complex parts, prototypes and high-precision components.
3-axis milling
What is 3-axis milling?
3-axis milling is a machining technique in which the workpiece moves along three linear axes: X (horizontal), Y (vertical) and Z (deep). This method is often used to machine flat surfaces and simple geometric shapes.
How it works
In 3-axis milling, the cutting tool (milling cutter) moves along these three axes to make cuts, grooves and holes. The workpiece is fixed on a table that moves along the X and Y axes, while the milling tool moves along the Z axis to make cuts of variable depth.
Benefits
- Cost-effectiveness: Less costly to install and maintain than more complex machines.
- Simplicity: easy to use and program.
- Accuracy: Good accuracy for simple geometries.
- Speed: Ideal for small and medium production runs.
Applications
3-axis milling is commonly used to manufacture mechanical parts, prototypes and components for sectors such as aerospace, automotive and electronics.
Limits
3-axis milling can be limited when creating complex shapes or geometries with undercuts, sometimes requiring manual repositioning.
4-axis milling
What is 4-axis milling?
4-axis milling adds a rotary axis to the machine, allowing the workpiece to rotate around the X axis. This feature makes it possible to machine parts with more complex shapes without having to manually reposition the part.
How it works
In addition to movements along the X, Y and Z axes, the rotary axis (A) can be used to rotate the part to access different sides in a single configuration. This makes it easier to produce cylindrical or asymmetrical parts.
Benefits
- Versatility: Enables machining of parts with more complex shapes.
- Precision: High precision for parts with complex details.
- Reduced set-up time: Fewer manual repositionings required.
Applications
4-axis milling is used for applications requiring cylindrical shapes, complex engravings and parts with detail on several sides. It is particularly useful in aerospace, automotive and gear manufacturing.
Limits
Although more flexible than 3-axis milling, 4-axis milling can still have limitations for very complex geometries or shapes with large undercuts.
5-axis milling
What is 5-Axis Milling?
5-axis milling incorporates two additional axes, generally referred to as the A and B axes, allowing complex, simultaneous movements in several directions. This makes it possible to machine parts with highly complex geometries in a single configuration.
How it works
Simultaneous movement of the five axes (X, Y, Z, A and B) enables the machine to create complex shapes with high precision. The cutting tool can move around the workpiece at different angles, making it easy to machine fine details and three-dimensional shapes.
Benefits
- Complexity: Capable of producing parts with highly complex geometries.
- Precision: High precision and excellent surface finish.
- Efficiency: Fewer repositionings required, reducing cycle times.
Applications
5-axis milling is ideal for parts with complex shapes in the aerospace, agri-food and medical manufacturing sectors. It is also used for precision parts in the automotive industry and in the production of complex moulds.
Limits
5-axis milling is more expensive and complex to program and maintain than 3- and 4-axis systems. It also requires specialist training to optimise its use.
2-axis turning
What is 2-axis turning?
2-axis turning is a technique where the workpiece rotates around the main axis (generally the Z axis), while the cutting tool moves along the X axis. This process is used to machine simple cylindrical parts.
How it works
In 2-axis turning, the workpiece is mounted on a chuck and rotates around the Z axis. The cutting tool moves along the X axis to remove material and create cylindrical, conical or grooved shapes.
Benefits
- Simplicity: Easy to use and program for simple cylindrical parts.
- Cost-effectiveness: Less expensive to purchase and maintain.
- Accuracy: Good performance for parts with simple geometries.
Applications
2-axis turning is used to manufacture cylindrical parts such as sleeves, rings and shafts in the automotive, mechanical engineering and industrial component manufacturing sectors.
Limits
It is limited to machining parts with simple geometries and cannot produce complex shapes or fine details.
3-axis turning
What is 3-axis turning?
3-axis turning adds an extra axis, usually called the Y axis, allowing the cutting tool to move in a direction perpendicular to the X and Z axes. This feature makes it possible to create more complex parts with internal and external shapes.
How it works
3-axis turning not only allows rotation of the workpiece around the Z axis, but also movement of the tool along the Y axis. This enables operations such as drilling deep holes and machining internal shapes.
Benefits
- Increased complexity: Enables complex internal shapes and details to be created.
- Precision: High precision for parts with more elaborate geometries.
- Versatility: Suitable for parts requiring multiple operations.
Applications
3-axis turning is used for more complex components such as engine parts, mounting brackets and parts with internal features in various industrial sectors.
Limits
3-axis turning can require more complex configurations and may be less suited to parts with highly detailed or asymmetrical geometries.
4-axis turning
What is 4-axis turning?
4-axis turning adds a fourth rotary axis, usually around the X or Y axis, giving greater flexibility for machining complex parts. This makes it possible to work on different sides of the part without repositioning it manually.
How it works
In addition to movements along the X, Y and Z axes, the fourth axis allows the part to rotate around an additional axis, making it easy to machine multiple faces in a single configuration.
Benefits
- Versatility: Capable of machining complex parts with several faces.
- Efficiency: Reduces the need for manual repositioning.
- Accuracy: Improves the accuracy of parts with multiple features.
Applications
4-axis turning is ideal for parts with multiple faces and complex shapes in the aerospace, automotive and industrial component manufacturing sectors.
Limits
Although more flexible than 2- and 3-axis turning, 4-axis turning can be more expensive and complex to programme and maintain.
Water jet cutting
What is water jet cutting?
Waterjet cutting is an industrial cutting technique that uses a very high-pressure jet of water, often mixed with abrasives, to cut a wide range of materials with great precision. The process is used for materials ranging from plastics and metals to stone and glass.
How it works
The waterjet cutting process is based on an ultra-powerful jet of water projected at a pressure of up to 6,000 bar. In some cases, an abrasive is added to the jet to cut harder materials. The material is cut without generating heat, thus avoiding any risk of thermal deformation.
Benefits
- Versatility: Able to cut almost any material
- Precision: Allows fine and complex cuts to be made with great accuracy.
- Cold process: No risk of heat distortion or material deterioration.
- Respect for the environment : Clean process, with little waste and no chemicals.
Applications
Waterjet cutting is used in a variety of sectors, including aerospace, automotive, construction and the craft industry. It is ideal for manufacturing complex parts, prototypes, decorative panels and technical components.
Limits
Waterjet cutting can be slower and more expensive for very thick materials or very large-scale production runs. In addition, some ultra-precise or specific applications may require complementary technologies.
Advantages of machining plastic parts
- Precision: Enables parts to be manufactured to very tight tolerances.
- Flexibility: Suitable for the production of prototypes, small series and large runs without the need for expensive moulds.
- Customisation: We can create bespoke parts tailored to the specific needs of each customer.
- Speed: Generally faster and less costly than injection moulding for limited series.
Conclusion
CNC machining of plastic parts is a versatile and precise technique that can meet a wide variety of industrial needs. Thanks to state-of-the-art equipment and the expertise of our technicians, we are able to produce high-quality parts tailored to your specific requirements. To find out more about our machining capabilities and to discuss your project, please contact us.
Re-machining of existing parts
Re-machining involves modifying existing plastic parts to adapt them to particular specifications. This includes adjustments such as cutting, engraving, adding functional elements or shapes.
- Choice of part: Select a part or a standard plastic enclosure that you wish to modify.
- Définition des Modifications : Indiquez les ajustements et les cotes nécessaires, les gravures, ou les modifications fonctionnelles.
- Machining and customisation: We make modifications to your specifications using our precision equipment.
- Quality control: We check each modified part to ensure that it meets the required standards.
You can request various modifications, such as :
- Machining new holes or openings
- Engraving or printing inscriptions
- Addition of fixings or functional elements
- Adjusting dimensions or shapes
Example of machining :
A typical example of re-machining would be the adaptation of a plastic housing for a new electronic application. You could choose a standard enclosure, define the necessary shapes for specific ports and connectors, and add logos or lettering to personalise the final appearance.
We can modify a wide range of new, used and even broken standard plastic parts, such as housings, panels and various components.
Re-machining is ideal for :
- Prototyping: Quickly adapt enclosures or parts for tests and demonstrations, as well as for series production.
- Small Series : Produce customised batches without the high costs of remanufacturing.
- Medium and Large Series : Adjust components, parts or even functionalities to meet new standards or integrate new accessories.
To obtain a quotation, contact us with details of the part to be modified and the specifications of the modifications required. We will provide you with a precise quotation in line with your request.
The lead time depends on the complexity of the modifications required and the quantity of parts. We will inform you of the estimated time when we quote for your project.
A project?
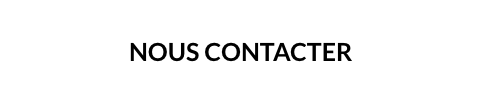