Komplette Bearbeitungswerkstatt
Die CNC-Bearbeitung von Kunststoffteilen ermöglicht es, eine Vielzahl von Komponenten mit bemerkenswerter Genauigkeit herzustellen. Dank unseres hochmodernen Maschinenparks und unseres hochqualifizierten Technikerteams sind wir in der Lage, Teile nach sehr genauen Spezifikationen für verschiedene Industriezweige herzustellen.
Die CNC-Bearbeitung von Kunststoffteilen ermöglicht es, eine Vielzahl von Komponenten mit bemerkenswerter Genauigkeit herzustellen. Dank unseres hochmodernen Maschinenparks und unseres hochqualifizierten Technikerteams sind wir in der Lage, Teile nach sehr genauen Spezifikationen für verschiedene Industriezweige herzustellen.
Unsere Fähigkeiten in der Kunststoffbearbeitung umfassen :
- Mechanische Teile aus technischem Kunststoff : Für bestimmte Werkzeugmaschinen oder Ausrüstungen konzipiert, können diese Teile Ersatz oder Komponenten für Ihre Produkte sein.
- Outillages sur-mesure : Nous fabriquons des outils spécifiques pour des applications particulières, tant pour l’industrie que pour l’artisanat.
- Teile, die mehrere Arbeitsschritte erfordern : Wir führen komplexe Bearbeitungen mit 3, 4 und 5 Achsen durch.
- Individuell gestaltete Vorderseiten : Maßgeschneiderte Ausschnitte für Bedienfelder, mit Gravur- und Digitaldruckoptionen.
Für die CNC-Bearbeitung sind keine Formen erforderlich, sodass wir ohne Mindestbestellmenge produzieren können. Wir können Anfertigungen :
- Einzeln oder als Prototyp
- In kleinen Serien
- In mittleren Serien
- In großen Mengen
All dies geschieht ohne zusätzliche Kosten.
Wie funktioniert die Bearbeitung von Kunststoffteilen?
Bei der maschinellen Bearbeitung von Kunststoffteilen wird Material aus einem Rohling entfernt, um die gewünschte Form und Größe zu erhalten. Hier ein Überblick über die Funktionsweise dieses Prozesses :
1. Auswahl des Materials
Der erste Schritt ist die Auswahl des richtigen Kunststoffmaterials für das herzustellende Teil. Dies hängt von den mechanischen, thermischen und chemischen Eigenschaften ab, die für die Endanwendung erforderlich sind. Zu den häufig verwendeten Kunststoffen gehören :
- PMMA (Plexiglas®/Altuglas®) : Transparent und steif, wird für optische Anwendungen verwendet.
- ABS : Schlagfest und leicht zu bearbeiten, wird in der Elektronik- und Spielzeugindustrie verwendet.
- PP (Polypropylen) : Ermüdungsbeständig, wird in Scharnieren und Lebensmittelbehältern verwendet.
- PC (Polycarbonat) : Sehr schlagfest und transparent, wird in Sicherheitsglas verwendet.
HDPE (Polyethylen hoher Dichte) : Chemikalienbeständig und abriebfest, wird in Rohren und Behältern verwendet.
2. Vorbereitung der Rohmünze
Der ausgewählte Kunststoff ist in der Regel in Form von Platten, Stangen oder Blöcken erhältlich. Diese Rohlinge werden auf annähernde Maße zugeschnitten, um die Bearbeitung zu erleichtern.
3. CNC-Programmierung
Der Bearbeitungsprozess wird von computergesteuerten Maschinen (CNC-Maschinen) gesteuert. Die Techniker erstellen ein CNC-Programm, das auf der technischen Zeichnung des herzustellenden Werkstücks basiert. Dieses Programm diktiert die Bewegungen des Schneidwerkzeugs und des Werkstücks auf mehreren Achsen.
4. Montage und Befestigung
Der Rohling wird mithilfe von Haltesystemen wie Vakuumtischen, Greifern oder bei Dreharbeiten auch in einem Futter fest auf dem Maschinentisch fixiert. Die richtige Fixierung ist entscheidend für die Genauigkeit der Bearbeitung.
5. Verwendung
Die Bearbeitung kann je nach Komplexität des Werkstücks durch verschiedene Arbeitsschritte erfolgen :
- Fräsen : Verwendet einen rotierenden Fräser, um Material abzutragen. Kann bei komplexen Geometrien mit 3, 4 oder 5 Achsen durchgeführt werden.
- Drehen : Das Werkstück dreht sich um eine Achse, während mit einem feststehenden Schneidwerkzeug Material abgetragen wird. Wird hauptsächlich für zylindrische Werkstücke verwendet.
- Bohren und Gewindeschneiden : Erstellen von Löchern und Ausbohren vorhandener Löcher. Anschließend Gewindeschneiden, um einen Gegenstand darin anvisieren zu können.
CNC-Maschinen führen diese Arbeitsschritte nach einem zuvor erstellten Programm aus und garantieren so eine hohe Genauigkeit und Wiederholbarkeit.
6. Ausgaben
Nach der Bearbeitung müssen die Teile möglicherweise nachbearbeitet werden, z. B. :
- Polieren : Um eine glatte, glänzende Oberfläche zu erhalten.
- Gravur und Druck : Um Beschriftungen oder Logos hinzuzufügen.
- Zusammenstellung : Integration von Einsätzen, Befestigungen oder anderen Komponenten.
7. Qualitätskontrolle
Ausgestattet mit einem Koordinatenmessgerät wird bei Artois Plastiques jedes bearbeitete Werkstück streng kontrolliert, um sicherzustellen, dass es die technischen Spezifikationen und Maßtoleranzen sowie die Formspezifikationen einhält. Dies kann auch genaue Dimensionsmessungen, Festigkeitstests und visuelle Inspektionen umfassen.
Maschinen und Bearbeitungstechniken
Bearbeitungszentrum
Was ist ein Bearbeitungszentrum?
Ein Bearbeitungszentrum ist eine vielseitig einsetzbare CNC-Maschine (CNC = Computerized Numerical Control), die verschiedene Arten von Bearbeitungen an Metall- oder Kunststoffteilen durchführen kann. Ausgestattet mit mehreren Werkzeugen und Bewegungsachsen kann ein Bearbeitungszentrum komplexe Arbeitsgänge wie Fräsen, Bohren, Gewindeschneiden und Schneiden durchführen.
Betrieb
Bearbeitungszentren sind so konzipiert, dass sie Rohteile aufnehmen und mit hoher Präzision bearbeiten können. Die Werkstücke werden auf einem Arbeitstisch befestigt und die Maschine führt die notwendigen Bewegungen nach einem CNC-Programm aus. Dieses Programm legt die Werkzeugwege und die auszuführenden Arbeitsschritte anhand der Spezifikationen des Werkstücks fest.
Vorteile
- Vielseitigkeit : In der Lage, eine breite Palette von Bearbeitungsvorgängen durchzuführen.
- Genauigkeit : Hohe Präzision dank digitaler Kontrollen und hochwertiger Werkzeuge.
- Wirksamkeit : Ermöglicht mehrere Operationen in einer einzigen Konfiguration, wodurch die Notwendigkeit manueller Neupositionierungen verringert wird.
- Verkürzung der Zykluszeiten : Dank der Möglichkeit, Arbeitsschritte zu programmieren, werden die Fertigungszeiten optimiert.
Anwendungen
Bearbeitungszentren werden in verschiedenen Branchen eingesetzt, z. B. in der Luft- und Raumfahrt, der Automobilindustrie und bei der Herstellung von medizinischen Geräten. Sie sind ideal für die Herstellung von komplexen Teilen, Prototypen und hochpräzisen Komponenten.
3-Achsen-Fräsen
Was ist 3-Achsen-Fräsen?
Das 3-Achsen-Fräsen ist eine Bearbeitungstechnik, bei der sich das Werkstück auf drei linearen Achsen bewegt: X (horizontal), Y (vertikal) und Z (tief). Diese Methode wird häufig zur Bearbeitung von ebenen Flächen und einfachen geometrischen Formen verwendet.
Betrieb
Beim 3-Achsen-Fräsen bewegt sich das Schneidwerkzeug (Fräser) entlang dieser drei Achsen, um Schnitte, Bearbeitungen, Nuten und Bohrungen zu erzeugen. Das Werkstück wird auf einem Tisch befestigt, der sich entlang der X- und Y-Achse bewegt, während sich das Fräswerkzeug entlang der Z-Achse bewegt, um Schnitte mit unterschiedlicher Tiefe zu machen.
Vorteile
- Rentabilité : Weniger kostspielig in der Installation und Wartung als komplexere Maschinen.
- Einfachheit : Einfache Bedienung und Programmierung.
- Genauigkeit : Gute Genauigkeit bei einfachen Geometrien.
- Schnelligkeit : Ideal für die Herstellung von Teilen in kleinen und mittleren Serien.
Anwendungen
Das 3-Achsen-Fräsen wird häufig zur Herstellung von mechanischen Teilen, Prototypen und Komponenten für verschiedene Branchen wie die Luft- und Raumfahrt, die Automobilindustrie und die Elektronikindustrie verwendet.
Grenzwerte
Das 3-Achsen-Fräsen kann bei der Erstellung komplexer Formen oder Geometrien mit Hinterschnitten an seine Grenzen stoßen, sodass manchmal eine manuelle Neupositionierung erforderlich ist.
4-Achsen-Fräsen
Was ist 4-Achsen-Fräsen?
Beim 4-Achsen-Fräsen wird der Maschine eine Rotationsachse hinzugefügt, sodass sich das Werkstück um die X-Achse drehen kann. Diese Funktion ermöglicht die Bearbeitung von Werkstücken mit komplexeren Formen, ohne dass das Werkstück manuell neu positioniert werden muss.
Betrieb
Zusätzlich zu den Bewegungen entlang der X-, Y- und Z-Achse kann das Werkstück mithilfe der Drehachse (A) gedreht werden, um in einer einzigen Konfiguration Zugang zu verschiedenen Seiten zu erhalten. Dies erleichtert die Herstellung von zylindrischen oder asymmetrischen Teilen.
Vorteile
- Vielseitigkeit : Ermöglicht die Bearbeitung von Werkstücken mit komplexeren Formen.
- Genauigkeit : Hohe Genauigkeit für Teile mit komplexen Details.
- Verkürzung der Einrichtungszeit : Weniger manuelle Neupositionierungen erforderlich.
Anwendungen
Das 4-Achsen-Fräsen wird für Anwendungen verwendet, bei denen zylindrische Formen, komplexe Gravuren und Teile mit Details auf mehreren Seiten erforderlich sind. Es ist besonders nützlich in der Luft- und Raumfahrt, der Automobilindustrie und bei der Herstellung von Zahnrädern.
Grenzwerte
Obwohl es flexibler ist als das 3-Achsen-Fräsen, kann das 4-Achsen-Fräsen bei sehr komplexen Geometrien oder Formen mit großen Hinterschnitten noch auf Einschränkungen stoßen.
5-Achsen-Fräsen
Was ist 5-Achsen-Fräsen?
Beim 5-Achsen-Fräsen werden zwei zusätzliche Achsen integriert, die üblicherweise als A- und B-Achse bezeichnet werden und komplexe, simultane Bewegungen in mehrere Richtungen ermöglichen. Dadurch können Werkstücke mit sehr komplexen Geometrien in einer einzigen Konfiguration bearbeitet werden.
Betrieb
Durch die gleichzeitige Bewegung der fünf Achsen (X, Y, Z, A und B) kann die Maschine komplexe Formen mit hoher Genauigkeit erstellen. Das Schneidwerkzeug kann sich in verschiedenen Winkeln um das Werkstück bewegen, was die Bearbeitung von feinen Details und dreidimensionalen Formen erleichtert.
Vorteile
- Komplexität : In der Lage, Teile mit sehr komplexen Geometrien herzustellen.
- Präzision : Hohe Genauigkeit und hervorragende Oberflächengüte.
- Effizienz : Weniger Neupositionierungen erforderlich, wodurch die Zykluszeiten verkürzt werden.
Anwendungen
Das 5-Achsen-Fräsen ist ideal für Teile mit komplexen Formen in der Luft- und Raumfahrt, der Lebensmittelindustrie und der medizinischen Fertigung. Es wird auch für Präzisionsteile in der Automobilindustrie und bei der Herstellung von komplexen Formen verwendet.
Grenzwerte
5-Achsen-Fräsen ist teurer und komplexer zu programmieren und zu warten als 3- und 4-Achsen-Systeme. Es erfordert außerdem eine spezielle Ausbildung, um seine Nutzung zu optimieren.
2-Achsen-Drehen
Was ist 2-Achsen-Drehen?
Beim 2-Achsen-Drehen dreht sich das Werkstück um die Hauptachse (normalerweise die Z-Achse), während sich das Schneidwerkzeug entlang der X-Achse bewegt. Dieses Verfahren wird verwendet, um einfache zylindrische Werkstücke zu bearbeiten.
Betrieb
Beim 2-achsigen Drehen ist das Werkstück auf einem Futter montiert und dreht sich um die Z-Achse. Das Schneidwerkzeug bewegt sich entlang der X-Achse, um Material abzutragen und zylindrische, konische Formen oder Nuten zu erzeugen.
Vorteile
- Einfachheit : Einfach zu verwenden und zu programmieren für einfache zylindrische Teile.
- Kosteneffizienz : Weniger kostspielig in der Anschaffung und im Unterhalt.
- Genauigkeit : Gute Leistung bei Teilen mit einfachen Geometrien.
Anwendungen
Das 2-Achsen-Drehen wird zur Herstellung von zylindrischen Teilen wie Hülsen, Ringen und Wellen in der Automobilindustrie, im Maschinenbau und bei der Herstellung von Industriekomponenten verwendet.
Grenzwerte
Sie ist auf die Bearbeitung von Werkstücken mit einfachen Geometrien beschränkt und kann keine komplexen Formen oder feinen Details herstellen.
3-Achsen-Drehen
Was ist 3-Achsen-Drehen?
Beim 3-Achsen-Drehen wird eine zusätzliche Achse hinzugefügt, die üblicherweise als Y-Achse bezeichnet wird und es dem Schneidwerkzeug ermöglicht, sich in einer Richtung senkrecht zu den X- und Z-Achsen zu bewegen. Diese Funktion ermöglicht es, komplexere Teile mit inneren und äußeren Formen zu erstellen.
Betrieb
Das 3-Achsen-Drehen ermöglicht nicht nur die Drehung des Werkstücks um die Z-Achse, sondern auch eine Bewegung des Werkzeugs entlang der Y-Achse. Dadurch können Operationen wie das Bohren tiefer Löcher und die Bearbeitung von Innenformen durchgeführt werden.
Vorteile
- Hohe Komplexität : Ermöglicht komplexe innere Formen und Details.
- Genauigkeit : Hohe Genauigkeit für Teile mit ausgefeilteren Geometrien.
- Vielseitigkeit : Geeignet für Teile, die mehrere Arbeitsschritte erfordern.
Anwendungen
Das 3-Achsen-Drehen wird für komplexere Komponenten wie Motorteile, Montagehalterungen und Teile mit internen Merkmalen in verschiedenen Industriezweigen verwendet.
Grenzwerte
Das 3-Achsen-Drehen kann komplexere Konfigurationen erfordern und ist möglicherweise weniger geeignet für Teile mit sehr detaillierten oder asymmetrischen Geometrien.
4-Achsen-Drehen
Was ist 4-Achsen-Drehen?
Beim 4-Achsen-Drehen wird eine vierte Drehachse hinzugefügt, die in der Regel um die X- oder Y-Achse rotiert, wodurch eine größere Flexibilität bei der Bearbeitung komplexer Werkstücke ermöglicht wird. So können verschiedene Seiten des Werkstücks bearbeitet werden, ohne dass das Werkstück manuell neu positioniert werden muss.
Betrieb
Zusätzlich zu den Bewegungen entlang der X-, Y- und Z-Achse ermöglicht die vierte Achse, dass sich das Werkstück um eine weitere Achse dreht, wodurch die Bearbeitung mehrerer Flächen in einer einzigen Konfiguration erleichtert wird.
Vorteile
- Vielseitigkeit : Kann komplexe Werkstücke mit mehreren Seiten bearbeiten.
- Effizienz : Reduziert den Bedarf an manuellen Neupositionierungen.
- Genauigkeit : Verbessert die Genauigkeit von Teilen mit mehreren Merkmalen.
Anwendungen
Das 4-Achsen-Drehen ist ideal für Teile mit mehreren Flächen und komplexen Formen in der Luft- und Raumfahrt, der Automobilindustrie und der Herstellung von Industriekomponenten.
Grenzwerte
Obwohl es flexibler ist als das 2- und 3-Achsen-Drehen, kann das 4-Achsen-Drehen teurer und komplexer in der Programmierung und Wartung sein.
Wasserstrahlschneiden
Was ist Wasserstrahlschneiden?
Wasserstrahlschneiden ist eine industrielle Schneidtechnik, bei der ein Wasserstrahl mit sehr hohem Druck, der oft mit Abrasivstoffen vermischt ist, verwendet wird, um eine Vielzahl von Materialien mit hoher Präzision zu schneiden. Dieses Verfahren wird für Materialien von Kunststoffen über Metalle bis hin zu Stein und Glas verwendet.
Betrieb
Das Verfahren des Wasserstrahlschneidens basiert auf einem extrem starken Wasserstrahl, der mit einem Druck von bis zu 6000 bar ausgestoßen wird. In manchen Fällen wird dem Strahl ein Abrasivmittel beigemischt, um härtere Materialien zu schneiden. Das Material wird ohne Hitzeentwicklung geschnitten, wodurch das Risiko einer thermischen Verformung vermieden wird.
Vorteile
- Vielseitigkeit : Kann fast jedes Material schneiden
- Präzision : Ermöglicht feine und komplexe Schnitte mit hoher Genauigkeit.
- Kaltverfahren : Kein Risiko von Hitzeverformung oder Materialveränderungen.
- Umweltfreundlichkeit : Sauberes Verfahren mit wenig Abfall und ohne Chemikalien.
Anwendungen
Das Wasserstrahlschneiden wird in verschiedenen Branchen eingesetzt, z. B. in der Luft- und Raumfahrt, der Automobilindustrie, im Baugewerbe und im Handwerk. Es ist ideal für die Herstellung von komplexen Teilen, Prototypen, dekorativen Platten oder technischen Komponenten.
Grenzwerte
Das Wasserstrahlschneiden kann bei sehr dicken Materialien oder sehr großen Produktionen langsamer und teurer sein. Darüber hinaus können einige ultrapräzise oder spezifische Anwendungen zusätzliche Technologien erfordern.
Vorteile der Bearbeitung von Kunststoffteilen
- Präzision: Ermöglicht die Herstellung von Teilen mit sehr engen Toleranzen.
- Flexibilität: Geeignet für die Herstellung von Prototypen, Kleinserien und Großserien, ohne dass teure Formen erforderlich sind.
- Individuelle Anpassung: Möglichkeit, maßgeschneiderte Stücke zu erstellen, die den spezifischen Bedürfnissen jedes Kunden entsprechen.
- Geschwindigkeit : Ein Prozess, der in der Regel schneller und billiger ist als das Spritzgießen für begrenzte Serien.
Schlussfolgerung
Die CNC-Bearbeitung von Kunststoffteilen ist eine vielseitige und präzise Technik, mit der sich eine Vielzahl von industriellen Anforderungen erfüllen lässt. Dank modernster Ausrüstung und dem Fachwissen unserer Techniker sind wir in der Lage, qualitativ hochwertige Teile herzustellen, die auf Ihre speziellen Anforderungen zugeschnitten sind. Wenn Sie mehr über unsere Bearbeitungsmöglichkeiten erfahren und Ihr Projekt besprechen möchten, setzen Sie sich bitte mit uns in Verbindung.
Nachbearbeitung vorhandener Teile
Bei der Nachbearbeitung werden bereits vorhandene Kunststoffteile verändert, um sie an bestimmte Spezifikationen anzupassen. Dazu gehören Anpassungen wie Schneiden, Gravieren, Hinzufügen von Funktionselementen oder Formen.
- Teileauswahl : Wählen Sie ein Standardplastikteil oder -gehäuse aus, das Sie bearbeiten möchten.
- Definition von Änderungen : Geben Sie die erforderlichen Anpassungen und Bemaßungen, Gravuren oder funktionalen Änderungen an.
- Bearbeitung und Anpassung : Wir führen die Änderungen nach Ihren Vorgaben mithilfe unserer Präzisionsgeräte durch.
- Qualitätskontrolle : Wir überprüfen jedes modifizierte Teil, um sicherzustellen, dass es den geforderten Standards entspricht.
Sie können verschiedene Änderungen beantragen, z. B. :
- Schleifen neuer Löcher oder Öffnungen
- Gravieren oder Drucken von Inschriften
- Hinzufügen von Befestigungen oder Funktionselementen
- Anpassen von Maßen oder Formen
Beispiel für die Wiederaufnahme der Bearbeitung :
Ein typisches Beispiel für eine Nachbearbeitung könnte die Anpassung eines Kunststoffgehäuses für eine neue elektronische Anwendung sein. Sie könnten ein Standardgehäuse wählen, die erforderlichen Formen für die spezifischen Anschlüsse und Stecker festlegen und Logos oder Beschriftungen hinzufügen, um das endgültige Aussehen anzupassen.
Wir können eine breite Palette an neuen, gebrauchten oder sogar gebrochenen standardisierten Kunststoffteilen modifizieren, z. B. Gehäuse, Platten und verschiedene Komponenten.
Die Nachbearbeitung ist ideal für :
- Prototyping : Schnelle Anpassung von Gehäusen oder Teilen für Tests und Demonstrationen ebenso wie für die Serieneinführung.
- Kleine Serien : Produzieren Sie personalisierte Chargen ohne die hohen Kosten einer Neuanfertigung.
- Mittelgroße und große Serien : Anpassen von Komponenten , Teilen oder sogar Funktionen, um neue Standards zu erfüllen oder neues Zubehör zu integrieren.
Um einen Kostenvoranschlag zu erhalten, wenden Sie sich an uns und geben Sie die Details des zu ändernden Teils und die Spezifikationen der gewünschten Änderungen an. Wir werden Ihnen einen genauen Kostenvoranschlag in Bezug auf Ihre Anfrage unterbreiten.
Die Bearbeitungszeit hängt von der Komplexität der gewünschten Änderungen und der Menge der Teile ab. Wir informieren Sie über die geschätzte Dauer, wenn wir Ihnen einen Kostenvoranschlag für Ihr Projekt machen.
Ein Projekt?
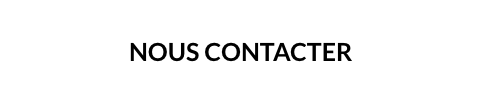